Table of Contents
It doesn’t take long searching the internet before you will find more than you ever wanted to know about how to design aluminum sand castings or how to do it better. It would not be hard to go on for several pages with general tips on how to make casting or how to do it better. The interesting thing about this process is that every step that can be found is a slight variation from what is generally considered to be wise counsel on how to do the job well.
What follows are general tips for how to design aluminum sand castings. These tips were created to help you to make manufacturing easier, improve the quality of your end product, and reduce the cost of producing a given project. Regardless of your goal in this process, there is even a secret ingredient or a “secret sauce” in improving every effort you make in aluminum sand casting. Not only will observing this secret make yours into a better aluminum sand casting foundry, but it will make the process more profitable as well.
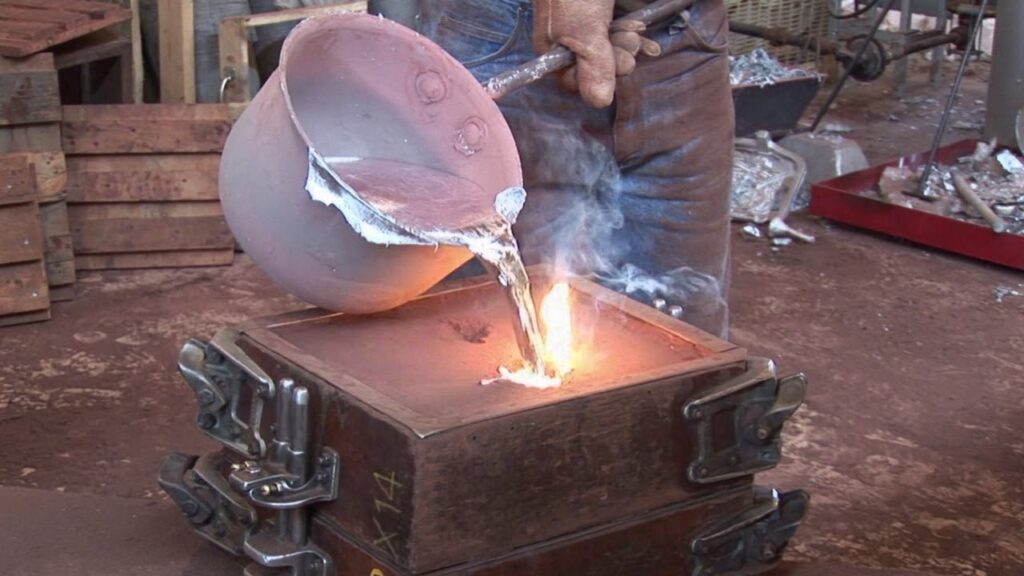
1. Add Strength, Not Mass
Aluminum sand casting really is a good example of making things better instead of bigger, but when it comes right down to it, many workers find themselves going for strength first. The trouble with this approach is that adding mass can cause a lot of problems that can otherwise be avoided, such as weight and hot spots. Adding design features can help with this too since it solves a problem without adding more material.
2. Consider Use
No part was ever intended to be used by itself. It is important to remember that the application of a part should be a prime consideration in its manufacture.
3. Use Draft for Thickness
Here again is another point at which good design can improve product quality. The parting line can be used to achieve the thickness desired.
4. Keep the Core Simple
Anyone with any experience with sand casting understands very well the influence that the parting line has on the final design. Keeping these are constant as possible is critical to success. It is also important at this point to introduce the “secret ingredient,” which is the sand.
Sand casting isn’t just a matter of loading a mold with sand that holds the object to be molded. The sand included can be any clean grade of sand, but when it comes to the sand that immediately touches the object to be molded, the key is to use sand that has been shifted to the finest degree possible. This is the sand you want between the object and the sand that holds everything in place. This will result in a better-quality final product.
5. Remember Secondary Machining
Once the casting process is complete and the final project has cooled and been removed from the sand, it’s important to understand there might be additional work that is called for to consider the project finished. This includes, most notably, additional machining that might be needed. Perform this machining on as few sides as possible, but take a close look at where it is needed. Performing this step well will not only improve the final product but also improve its quality.